«Moldeo por inyección asistida con gas (GAIM)
Introducción
La penetración de un fluido en una cavidad ocupada completamente por un líquido de diferente naturaleza es un problema de interés práctico, ya que tecnológicamente puede tener numerosas aplicaciones como la eliminación de aceites en superficies porosas, el revestimiento de fibras por líquidos, el acabado de productos cerámicos o la fabricación de cuerpos huecos mediante el moldeo asistido por gas.
Precisamente este es principio en el que se fundamenta el moldeo por inyección asistido por gas (GAIM: Gas-assist injection molding), que está siendo actualmente utilizado para la fabricación de piezas acabadas a partir de polímeros fundidos, en cuyo caso, se hace fluir agua o un gas (generalmente nitrógeno) dentro de la masa fundida de un polímero para que adquiera la forma final de la cavidad de moldeo correspondiente.
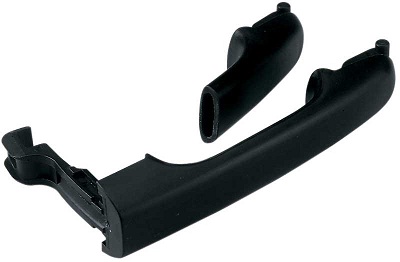 |
Pieza producida mediante inyección asistida por gas (por tobera) |
La fabricación por inyección de piezas plásticas moldeadas por esta técnica conlleva tres modificaciones del proceso convencional de moldeo:
– Llenado completo o parcial dela cavidad de moldeo con el polímero fundido
– Penetración del gas a través de la masa fundida
– Expulsión de la pieza.
Con estas modificaciones la presión aplicada por el gas sobre el material fundido se trasmite con pérdidas mínimas, reduciendo el consumo de potencia y aumentando la calidad del producto acabado.
El origen de esta tecnología (GAIM) se remonta prácticamente a cuatro décadas, desde el registro de la primera patente por Friederich, en Alemania en 1975, y de Olabisi en EEUU en 1979. Su desarrollo comercial comienza en los 80’s, y desde entonces diferentes empresas han implantado esta técnica para la fabricación de sus productos debido entre otras razones a:
– La versatilidad para fabricar distintas geometrías
– La posibilidad de fabricación de piezas de mayores dimensiones
– El mejor acabado superficial
– La menor contracción y consecuencia la mejor estabilidad dimensional
– Posibilidad de fabricar piezas con paredes más delgadas
– Los ciclos de fabricación más cortos
– Ahorro sustancial de material
El modelo asistido por gas ha permitido la fabricación de piezas que mediante el moldeo por inyección convencional serian imposible de lograr, por ejemplo piezas con inserciones metálicas sobre paredes delgadas, parachoques, carcasas de radiadores, o bien piezas con grandes áreas superficiales como carcasas de fotocopiadoras, televisores y electrodomésticos en general, o piezas que convencionalmente se exponen a grandes esfuerzos mecánicos como pedales de automóviles, cuyas formas y diseños complejos requieren de resistencia a la flexión y a la torsión.
Algunas variantes de esta técnica son las siguientes:
Blow-up : Se insufla nitrógeno dentro de una masa de material polimérico fundido introducido en el molde, y por efecto de la entrada de gas, la masa fundida se va expandiendo hasta chocar con las paredes del molde, conformándose finalmente el material.
Blow-out : La cavidad de moldeo se llena con material fundido y posteriormente se inyecta nitrógeno de manera que cuando el gas se expande, el fundido en exceso sale a contracorriente, por la misma entrada del molde, haca el cilindro de preplastificación.
En sus inicios el GAIM pretendió ser la respuesta para la fabricación de cualquier pieza a precios económicos con importantes ahorros de tiempo y material. Sin embargo, la experiencia ha demostrado que no todas las piezas pueden moldearse por esta técnica, especialmente aquellas que no tienen una dirección preferencial de flujo de forma que el gas no puede deformar la masa fundida de polímero en un sentido definido, por ejemplo piezas planas como tapas, vasos y en general productos para envasados. Por esta razón, actualmente es posible encontrar un gran número de estudios y programas de software que permiten obtener con buena aproximación la forma de propagación del gas durante la expansión de la masa fundida. Sin embargo, estas aproximaciones fallan respecto a la predicción de propiedades de la pieza fabricada, lo que representa, en este sentido, una buena oportunidad para el desarrollo de nuevas investigaciones.
Consideraciones técnicas
Existen una serie de consideraciones técnicas que deben tenerse en cuenta para el manejo de esta tecnología. Primeramente, habrá que considerar la diferencia de viscosidades entre el polímero fundido y el gas, que generalmente es nitrógeno, y segundo, que el gas es compresible. Estas diferencias físicas hacen que tan pronto como se inyecte el gas en un punto específico:
– La masa fundida comience a moverse a través del molde, y tan pronto encuentre alguna resistencia (la pared del molde) el gas no fluirá más hacia ese punto, sino que se desviará hacia donde no encuentre resistencia alguna, con lo cual se asegura que el espesor de la pared será virtualmente constante, y determinado casi exclusivamente por la geometría de la propia cavidad de moldeo.
– A diferencia del moldeo por inyección convencional, la compresibilidad propia del gas, hace que una vez inyectado en la masa del fundido, se genere la expansión sin control de ésta dentro de la cavidad de moldeo.
– El nitrógeno siga la trayectoria de menor resistencia. Por lo tanto es importante cuidar la cantidad de masa de prellenado, porque pequeñas diferencias pueden conducir a diferencias importantes en la distribución de gas, de ahí que la reproductibilidad de las piezas estará directamente relacionada con la precisión del diseño geométrico del molde.
En función del diseño geométrico del molde, la propagación de la burbuja puede variar entre ciclo y ciclo. De ahí la necesidad de que el diseño del molde sea muy preciso y ajustado al proceso
Materiales plásticos utilizados
En general cualquier tipo de termoplástico que se emplee para la fabricación de piezas por inyección, puede utilizarse para la fabricación de piezas por GAIM, entre otros PP, ABS, PE, SAN, PPO, PBT e inclusive formulaciones con rellenos y refuerzos del tipo de fibra de vidrio. Por supuesto, los parámetros de procesado deberán seleccionarse de acuerdo a la forma del molde y de las características del polímero seleccionado. Así mismo, resulta evidente que los materiales semicristalinos presentan, por su menor viscosidad en estado fundido, mejores características de flujo y facilidad de conformado con respecto de los polímeros amorfos.
Requisitos del gas
El GAIM demanda altas presiones y óptimo control de las mismas durante el proceso, por lo que se requiere de complejos sistemas de válvulas que regulen presiones generadas por los compresores que pueden alcanzar valores de hasta 30 MPa (4400psi). Los puntos de inyección de gas pueden situarse en la misma entrada de la cavidad de moldeo, o bien separadas de esta, todos es función del diseño del molde y del tamaño de la pieza a fabricar.
La inyección de gas a la cavidad de moldeo a través de la misma boquilla de entrada de material fundido, normalmente se utiliza cuando la pieza es axialmente simétrica, inclusive puede ser utilizada para el caso de moldes multi-cavidades.
Cuando las piezas a fabricar no sean alargadas es preferible colocar la entrada de gas en posición diferente a la entrada de la cavidad de moldeo. En este caso, la entrada de gas puede colocarse en puntos estratégicos para obtener productos con prestaciones específicas localizadas, lo que les infiere alta calidad como producto acabado.
Los gases utilizados en esta tecnología suelen ser nitrógeno (N2), o anhídrido carbónico (CO2) en menor medida.
Proceso
Debido a que el proceso requiere inyectar en una misma cavidad de moldeo dos materiales muy distintos entre sí, los ciclos de producción difieren respecto al moldeo por inyección convencional. Desde este punto de vista, resulta evidente que la inyección de ambos fluidos a la vez es prácticamente inviable por lo que los ciclos de ambos deben ser superpuestos en función de las secuencias de fabricación de una pieza dada. Así, el gas solo puede inyectarse una vez que la masa de polímero fundido sea introducida dentro de la cavidad de moldeo, y la expansión de la misma comienza cuando la presión del nitrógeno es mayor que la presión del propio fundido.El proceso convencional de moldeo por inyección asistida con gas consta de las siguientes etapas:
– Cierre del molde
– Inyección del plástico fundido
– Inyección del gas en la masa de fundido
– Mantenimiento de la presión de gas durante la solidificación
– Reducción de la presión del gas
– Apertura del molde
– Expulsión de la pieza
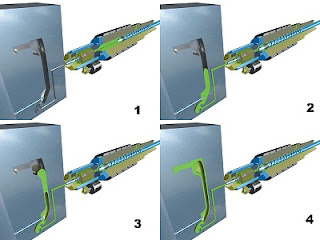 |
Secuencia del llenado de la cavidad del molde en el proceso de inyección asistido por gas (por tobera) |
La correcta fabricación de piezas mediante GAIM por soplado en fundido (blow-up) requiere necesariamente un correcto volumen de fundido pues en caso contrario pueden ocurrir dos tipos de fallos:
– Un llenado insuficiente puede propiciar la rotura de la burbuja.
– Un exceso de material fundido puede alterar el ciclo del proceso entre cada pieza fabricada.Es recomendable que el tiempo que transcurre entre la pre-inyección del fundido y la inyección de gas a esta masa sea lo más corto posible, porque los cambios de viscosidad en función del tiempo de residencia en la cavidad de moldeo pueden generar problemas de acumulaciones puntuales de material, y con ello defectos en la pieza acabada.Por el contrario, en el caso del moldeo asistido por soplado a contracorriente (blow-out), las ventajas son evidentes, ya que la superficie de moldeado se forma más limpiamente a través de la cavidad inicialmente llena. En este caso, la inyección subsecuente de gas no genera problemas sobre la superficie del moldeado. No obstante, los espesores de pared residuales en este segundo caso, tienden a ser algo más grandes que mediante blow-up.
Aunque es bien conocido que la viscosidad de los polímeros fundidos sigue un comportamiento del tipo Arrhenius con respecto a la temperatura, la influencia de esta sobre los espesores de pared tiene más bien poca influencia, así, en el caso de ensayos con policarbonato, la experiencia ha demostrado que el espesor de pared es prácticamente constante cuando el molde se calienta desde 55 a 95ºC, sin embrago cuando se utiliza el mismo molde y se emplea nylon reforzado con distintas concentraciones de fibra de vidrio, el espesor de pared puede disminuir hasta menos de un 50% cuando se aumenta el contenido de fibra de 0 a 50%.
Desventajas
La GAIM sin embargo tiene limitaciones y entre las más conocidas se encuentran las siguientes:
– Costos adicionales debido al empleo de gas, así como a los dispositivos de control de inyección y en su caso los honorarios correspondientes a las licencias de uso
– La imperfecta reproductibilidad debido a la diferencia aerodinámica de las distintas cavidades.
– En caso de piezas de seguridad, se requieren espesores de pared más gruesos lo que conlleva elevar los gastos de consumo de materia prima.
– Mayores limitaciones respecto a los parámetros de control de calidad de la materia prima.
– Moldes con mayores requisitos de diseño que los convencionales de moldeo por inyección.
– Mayor gasto de inversión desde la puesta en marcha hasta el desarrollo de la capacidad completa de la tecnología GAIM.
– Desarrollo y selección de formulaciones de moldeo más difíciles.»
fuente:©http://tecnologiadelosplasticos.blogspot.com.es/2012/05/moldeo-por-inyeccion-asistida-con-gas.html